You are here
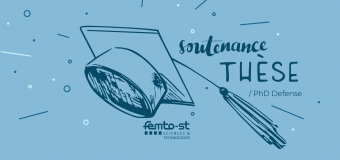
Pierre RANC "Contribution to the development of an Externally Heated Valve Engine"
12 juillet 2019 à 10hAmphithéâtre n°3, bâtiment D, 19 avenue du Maréchal Juin, 90000 Belfort
PhD work : «Contribution to the development of an Externally Heated Valve Engine with metal bellows. Theoretical study, conception, build and experimental characterization. »
Abstract:
Specifically, it focuses on the development of a dedicated dynamic model in order to predict a wide range of the engine's capabilities. This mathematical model is made up of thermodynamical and mechanical equations. The flow which passes through the compressor valves and expander valves is modelled on the Barré-de-Saint-Venant equation. A parametric analysis of the compressor ratio, mechanical load, temperature or polytropic coefficient is done in order to assess their effects on the engine's kinematics. Furthermore, the conception and the build of a test bench is made.
It consists of metal bellows that aim to replace the traditional cylinder and piston. The compressor is linked to the expander from a lever which allows the reduction of the pressure force during the expansion stroke. It also gives the possibility to alter the working volume. Pressure, force, flow and temperature sensors are placed on the engine at strategic points in order to study it. A microthermocouple is used to monitor the temperature signal in the compression and expansion phase.
Initially, the engine is tested at ambient temperature to give a point of reference. Electrical heaters are used to increase the expansion temperature starting point above 450°C. It appears that a heat flow in the cylinder head, cools down the warm airflow coming from the heater to 160°C in the best case scenario.
The experimental results show a really good agreement with the model, particularly if we consider the engine dynamic in terms of pressure, displacement or volume. A compression cooling system is also added to the test bench in order to reduce energy needs. In all cases, the temperature during the compression is always lower with the injection of water mist. And finally, intake expander pipes and discharge compressor pipes are connected to measure the pressure loose and temperature fluctuations of the airflow between the bellows.
The studied technology is promising particularly thanks to the use of bellows that allow a superior exchange of heat, as well as avoiding leaks and friction.
Jury members:
- Ms Grosu Lavinia Assistant Professor HDR at University of Paris Nanterre, LEME Reporter
- Mr Stouffs Pascal, Full Professor at University of Pau and Pays de l’Adour, LaTEP, Reporter
- Mr Vincent Lemort, Professeur à l’Université de Liège, Laboratoire de Thermodynamique, B49, Reviewer
- Mr Eric Delacourt, Assistant Professor at University of Valenciennes and Hainaut-Cambrésis, ENSIAME, Reviewer
- Mr François Lanzetta, Professor at l’University of Franche-Comté, FEMTO-ST laboratory, PhD Supervisor
- Mr Philippe Nika, Professeur at l’University of Franche-Comté, FEMTO-ST laboratory, PhD Co-Supervisor
- Mr Eric Gavignet, Assistant Professor at Université of Franche-Comté, Supervisor
- Mr Guillaume Layes, Assistant Professor at Université of Franche-Comté, Supervisor
- Mr Thibaut Cartigny, General manager of "Ananké" company, Invited
Location : amphithéâtre n°3 du bâtiment D de l'IUT Belfort-Montbéliard Département Génie Civil et Construction Durable, 19 avenue du Maréchal Juin, 90000 Belfort.
A video clip that resume this thesis subject added with an engine assembly time lapse is available following this link: https://youtu.be/Ocs8sOcMQZY